How Today’s New 3D Printers Open Up New Possibilities to Photographers
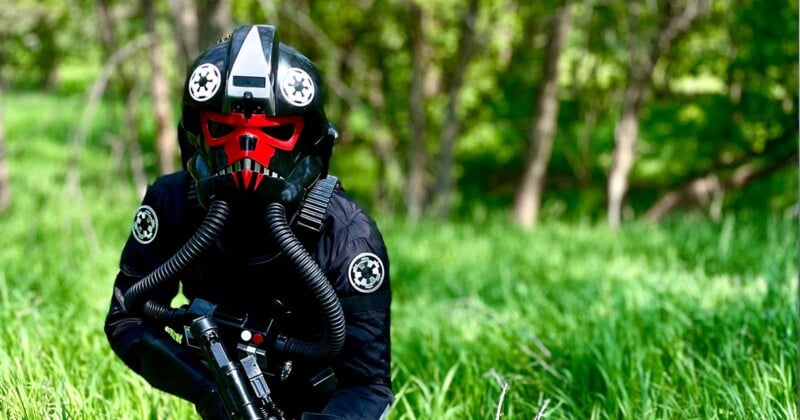
When I opened the box containing the Loupeck CT editing station for my review earlier this year, I immediately looked to see if it had a stand. Designed to sit flat on the desk, the orientation of the Loupedeck wasn’t particularly comfortable on my wrist. It did not.
Ordinarily, I’d probably have continued to use it lying flat on my desk and grumbled to myself each time I used it. Alternately, I’d have tried to put something under it to shim it up, which would inevitably end up wobbly or flimsy.
Instead, I designed and printed an angled base on a 3D printer to hold the Loupedeck at a better angle, and now, after a few test prints, I’ve got a stand oriented precisely how I want.
The total cost of the solution, including the two test prints I made before finalizing the design, was $1.35, with a total of three hours from conception to completion. Much of that time was printing time, during which I was working on articles and editing images.
That printing cost, along with the whole roll of filament I used, was paid for by the extra money I make selling printed objects on Etsy. This excellent side hustle utilizes the free time on my printers between fixing things or making tools.
There are several significant ways in which 3D printing can help the photographer and photographer and even help add some revenue: fixing problems, organizing and storing, making props, and making additional income.
A New Era in 3D Printing
3D printers are often considered hobbyist devices: complicated and finicky devices primarily good for making fidget spinners, toys, and waste. For decades, 3D printing has been the modern-day equivalent of HAM radios, with aficionado spending hours tweaking and tuning them.
Until recently, 3D Printers were slow as dirt, with printing times for complex objects stretching across days. 3D printers were already maturing and getting easier to use (and faster) when a newcomer company entered the market with a speedy, accurate, and very-affordable set of printers.

The new X1C and P1P printers from the upstart Bambu Lab lit a fire under the other manufacturers, and suddenly, the market is full of affordable printers that are up to 10-times faster than previous models and that require less tweaking of settings and parameters to use.
To be fair, 3D printers were already starting to get their most significant updates in many years, with faster processors and better firmware to control the devices. Still, Bambu Lab’s entrance on the scene moved up timetables.
For the last six months, I’ve been working with several 3D printers in the studio and doing reviews on them on my YouTube channel, and now consider them a must-have part of my workflow.
Different Printers, Different Uses
There are two completely different types of devices in the 3D printer world: filament and resin.
Filament printers are the most common type of 3D printer and are probably what you think of when you hear the term. These printers use plastic spools, and different materials are available for other jobs. PLA is the most common and affordable filament, but these printers can print flexible plastics and even ABS, the type of plastic used in automotive construction.
Filament printers are what I’m referring to most of the time. I’ll discuss 3D printers, and they are the most versatile and easiest-to-use printers.
The second type of printer is a resin printer, which uses liquid resin and UV lighting to harden resin layers into a final object. Resin printers are best used for models and fine-detail pieces. While there are different types of resin, the selection is less versatile in types of colors than filament printers.
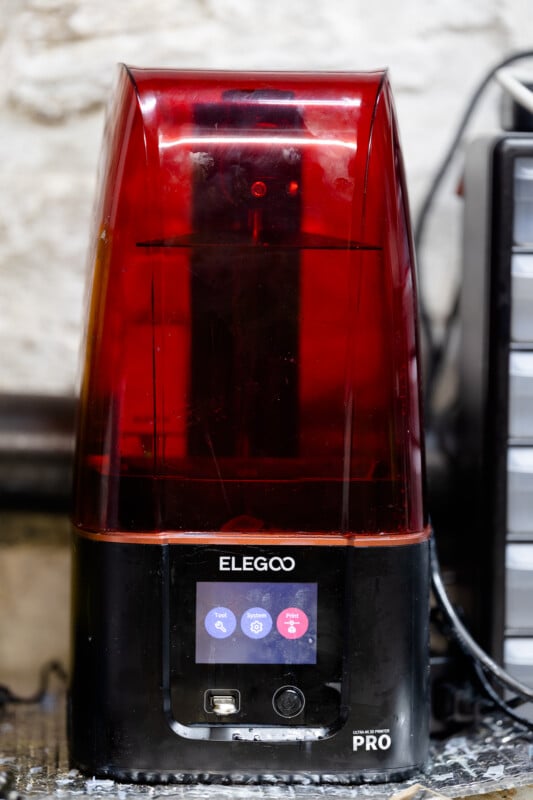
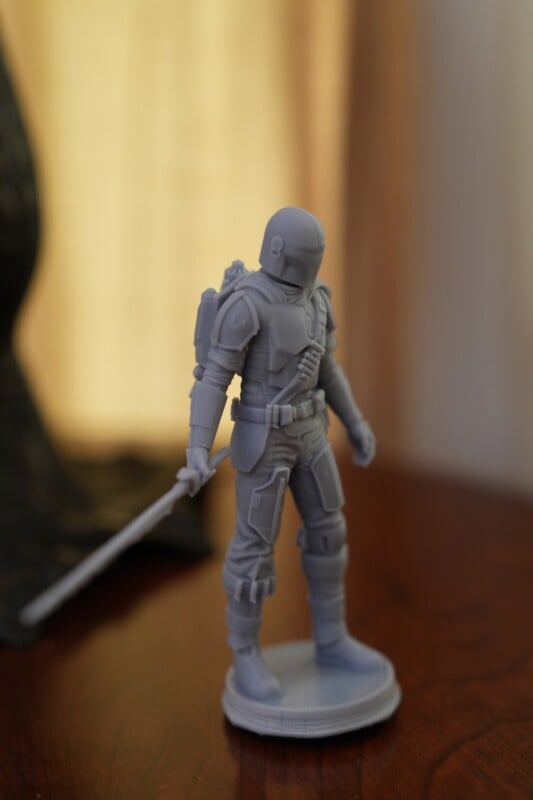
Testing Different Uses
The first printer to arrive in our house, the device that set off my 3D printing obsession, was the Prusa Mini+, a solid-yet-small starter printer that my son’s grandmother got for his combined birthday and Christmas present.
The first 3D printer you get seems like magic, and we’d sit and watch the printer working, captivated by it, making something before our very eyes, like some super-slow replicator from Star Trek.
This printer motivated my son to pick up and learn the program Blender, and now at 12, he’s creating blasters from Star Wars, spaceships, and even a Mother’s Day present for my wife. Motivating a kid to learn one of the most powerful 3D modeling and animation programs is enough to get a printer.
While durable, the Mini+ is imagination-constraining small, so I contacted Bambu Lab to see if I could get a review unit. They were more than happy to send a unit, so I also contacted Elegoo and Creality, which are significant players in the 3D printer space, and started to put them into daily use while I tested them for my channel.
The Bambu P1P is the stripped-down version of the company’s original flagship, the X1C. The company removed the outer enclosure and other industrial-centric features to create the $700 P1P.
Bambu Lab removed all the setup and configuration typically required in setting up a 3D printer. Many printers must be leveled and tweaked to get the best prints possible. Bambu Lab turned this idea on its head and designed most of the setup and configuration steps to be performed automatically by the device.
The $700 price is higher than most other printers in the market, but forums are filled with people who talk about the savings in time and effort resulting from the industrial design of the P1P and X1. My test unit is a workhorse that has been running near continually for six months.
The Bambu P1P is the best return on investment in 3D printing. The higher price (relative to entry-level models) is returned in reduced printing time and higher-quality output. Prints routinely take half the time on the Bambu or less than on other printers. A recent print that would have taken 24 hours on a slower printer finished on the Bambu in around 10 hours.
This has been particularly helpful for the “side hustle” 3D printing I’ve done, and I’m using it to produce prints for
With the Bambu price higher price than many newcomers might want to spend, I also wanted to look at a more “affordable” printer that would be good for the first-time buyer on a budget. Elegoo sent the Neptune 3 Pro printer, and at under $300, in my review of it, I declared it the best entry-level printer on the market.
Then Elegoo announced the new Neptune 4 and Neptune 4 Pro printers, which are only slightly higher priced than the version three printers I looked at. These printers use a different firmware than previous generation printers, allowing them to perform up to five times faster than their predecessors. Those printers are on the way, and unless something tragically wrong happens with these updates, they’ll become my pick for best entry-printer.
Elegoo also sent the Mars 3 Pro, a 4K resin printer that is under $200 and is probably the best introduction to resin printing. I have to admit I haven’t quite gotten into the groove with resin printing since I often turn to 3D printing for solutions to functional problems. I’ve finally begun producing some high-quality results from the printer, and it’s perfect for props or items where the least amount of finishing work is required.
Resin also requires liquid chemicals, a wash, and a curing pass to harden the UV-sensitive resin, which makes it the most like darkroom printing, and I find the process very familiar.
Resin printers are superb at fine details and models, and they use standard LED displays to “draw” the images that then get hardened into the resin. The higher the resolution of the display, the more detail the models can have. A 4K printer like the Mars 3 Pro makes a highly-detailed print, and now 12K printers are starting to hit the market.
The print bed’s size constrains the print size in the flat x and y axes and the three-dimensional Z (up-down) axis. The Bambu and the Neptune Pro have relatively similar dimensions, with the Bambu the largest at 256x256x256 millimeters and the Neptune Pro 3 at 225x225x280 millimeters.
To create bigger pieces, such as large cosplay helmets and props, I also reviewed the Creality Ender 3 Max Neo, a large-volume printer with a max size of 516x582x590 millimeters. The Ender 3 is one of the longest-running and most common printer lines and the oldest technology. This printer was the one closest to the stereotype of traditional 3D printing, requiring a lot of tinkering on my part. I printed dozens of things on the Bambu and the Elegoo Neptune while tweaking the Ender. But the final results are excellent, and the build volume is massive. It was big enough to print complete cosplay helmets in one shot.
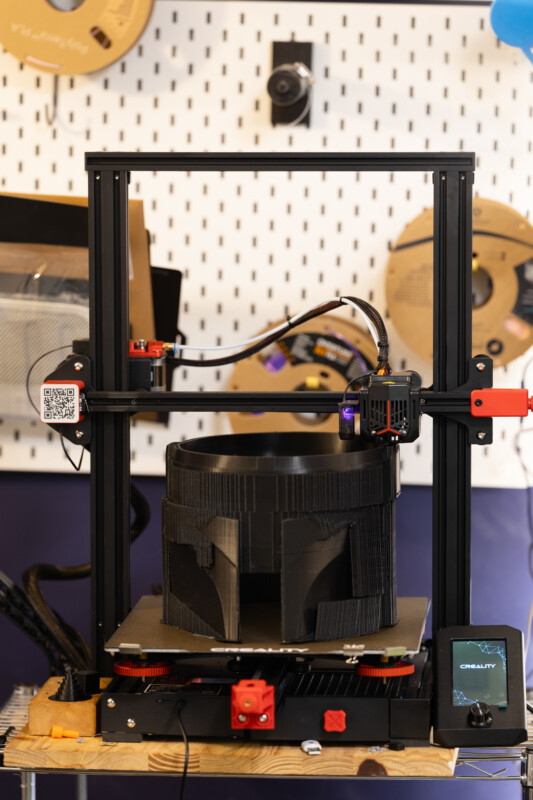

Building Solutions
The most common use of my printers in the studio is to build accessories or parts to modify or improve another product. The base for the Loupedeck CT is a prime example, with a little bit of 3D design and some printing, and I had a fix (If you have a Loupedeck and a 3D printer, you can download it here.)

Another quick fix was an adapter I made to use the Parrot Telecaster with the Sony ZV-1. Without a filter mount on the ZV-1, it’s impossible to connect the camera to the Parrot, yet that’s a camera I take whenever I’m on the road, and I often use it for talking heads when I’m testing other cameras. A tripod mount is available that allows you to use the Parrot with the ZV-1, but it costs around $35. My solution took about $3.00 in materials.

I’ve also used the printer to make replacement ARCA-Swiss and Manfrotto tripod plates, making it easier to switch quickly between cameras no matter which tripod I’ve grabbed. I picked up a five-pack of tripod screws on Amazon for $9.00 and printed out a handful of adapter plates for under $5.00.
I also found and printed a triple-cold-shoe mount, allowing me to test multiple microphones side-by-side, which I typically use to mount an iPhone, mic, and light onto a tripod.

The 3D printers get pressed into service around the house too. I’ve printed replacement pieces for missing door hardware in my home, made custom height shims for furniture, and printed parts missing from a piece of exercise equipment someone gave me.
A quick and easy (and free) program to get started with is Tinkercad, and I use it for many of my simple designs. The interface is designed for beginners and is like playing with building blocks in that you can lay out shapes and stack them, attach them, and cut holes out of them quickly.
Organization
I am a clutter hound. My desk often looks like a UPS truck exploded, leaving SD cards, lenses, and other gear strewn across. I am notoriously bad at putting things in their place because I’m never quite sure what their place is.
An open-source storage system called Gridfinity has come to my rescue. Gridfinity consists of a standard base and standard accessory size. People make and publish their designs to hold everything from drill bits to lipstick to knives.
I’ve been using Gridfinity to store my photographic gear at arm’s reach and to give items a place to return to. Gone is the clutter of SD and CFE cards on my desk, instead each is arranged in its cube in the Gridfinity base, along with filter holders, a holder for my camera batteries, lens holders, and even a place to stick my ZV-1 when it’s not in use.
Gridfnity was designed by the quite-possibly-insane-and-highly-entertaining YouTube creator Zack Freedman and has since gone open-source. There are thousands of pre-made Gridfinity designs available.
Another popular organizational tool is Ikea’s oblong-hole pegboard Skadis. Plenty of 3D-printed holders are available for Skadis, and it’s a great storage solution for things like diffusers, reflectors, and anything that could hang by a peg.
Giving Props
For many photographers, 3D printers are also part of the creative process. 3D printers make it possible to print props and set pieces and create models for storyboarding.
For photographer Gabrielle McCann, 3D printing has given her a new photographic subject.
“My husband Jamie is the maker in the family,”Says McCann. “He was already a talented painter before he got his first 3D printer (little did I know this purchase would change our lives forever). His career goals changed from studying international relations, terrorism, and victimology to becoming a prop maker for Galactic Armory — a 3D cosplay design house. Prop making and cosplay is what makes him happy. He introduced me to the world of cosplay, and as a writer I loved the way embodying my favorite characters gave me a different kind of access to stories I love. We joined the 501st costuming group together and it’s become such an amazing thing to share.”
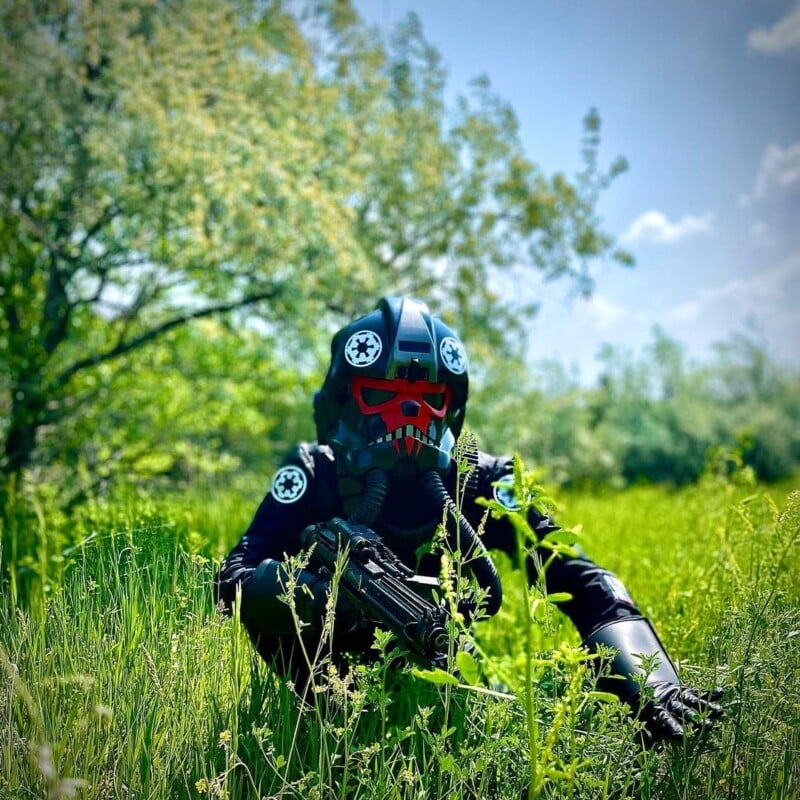
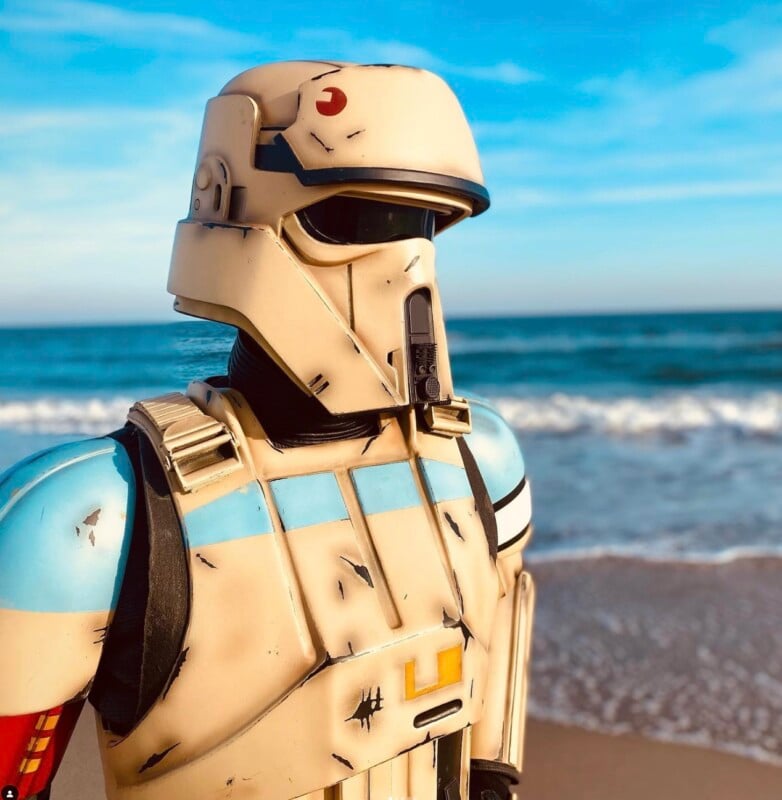
“I minored in photography and film in college and I have always loved the medium,” she adds. ” As an adult I lost connection with the hobby, but the beautiful armor that Jamie has made has given me a reason to pick it up again. My interest is to specialize in outdoor or “on site” cosplay photography (rather than studio) and I love capturing moments with a lot of movement, mimicking a cinematic still. I’m at the beginning of my journey with cosplay photography, but I would love to expand in the future and photograph more people in cosplay from any fandom. My hope is to make people feel like they are the main character in their own movie. It’s a powerful feeling!”
Side Hustle
The final thing that I have been using my 3D printer for is a side business of printing 3D objects for people in my town and selling items on Etsy.
Few other tools in a photographer’s studio allow them to make extra revenue while they sleep, but it’s possible with 3D printers.
Several people I know on Reddit and Discord are so busy selling items to people who need prototypes or final pieces that they gave up their day jobs and now run print farms. That’s not my personal goal, but it shows that the technology has promise and can help increase the value of a photographic studio.
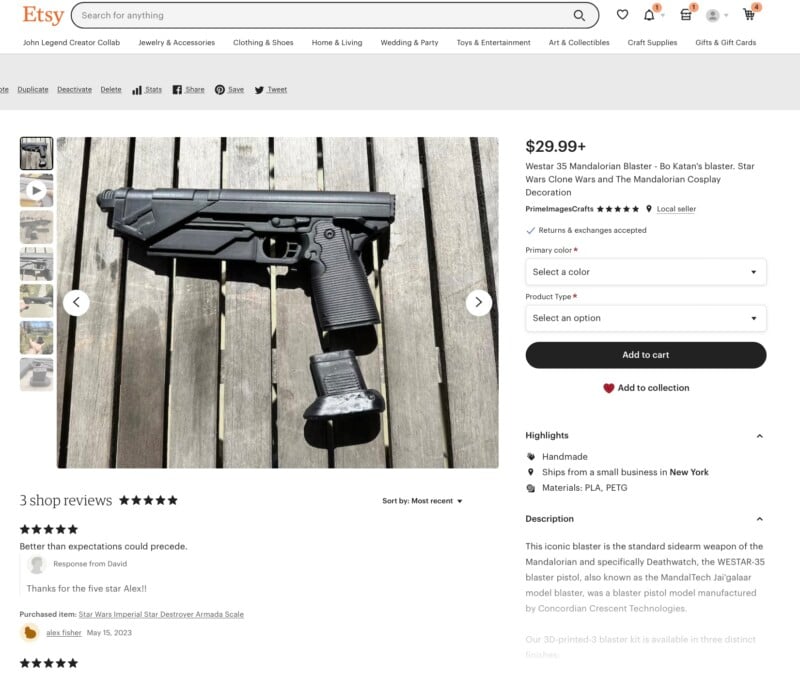
Rapidly Improving Market
The 3D printer market is about to grow rapidly thanks to easier-to-use devices like the Bambu P1P and X1C and the Elegoo Neptune printers. It’s only been around a year since the X1C debuted, and in that time, the other companies in the 3D space, companies that upgraded products at a plodding pace, have suddenly started to release more powerful, faster, easier-to-use, and cheaper printers.
The photography and video studio that uses 3D printing can now solve problems, make props, and even earn extra revenue at an exceptionally sensible investment of money and time.
Even if it’s only used a few times a year, a 3D printer is an excellent investment in creative possibilities and up-cycling gear and equipment.